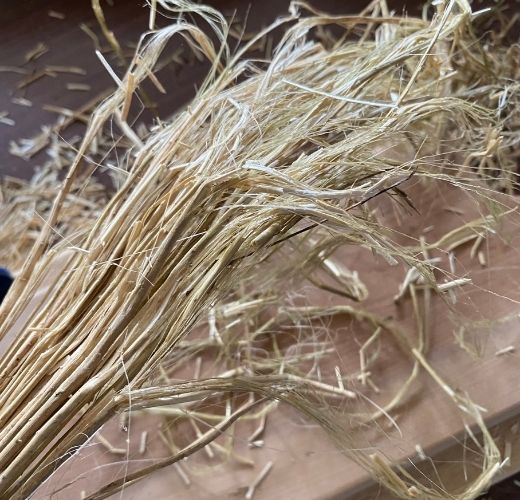
夏服、キッチンタオル、バッグ……私たちの身の回りには、リネンで作られたものがいっぱいありますよね。この記事では、リネンが原材料の亜麻(フラックス)から生地になるまでを解説いたします。身近なリネンの「できるまで」を、一緒に追いかけてみませんか?
リネンの原材料は亜麻(フラックス)
リネンができるまでを見ていく前に、原材料である亜麻(フラックス)についてご紹介いたします。フラックスとは亜麻科の植物です。日本語では亜麻と呼んでいます。十分に育ったフラックスの茎の繊維を加工することで、リネンの糸が出来上がります。それをさらに加工すれば、見慣れた洋服やテーブルクロスへと姿を変えていくのです。
亜麻(フラックス)とは
フラックスは亜麻科の一年生植物です。植物の亜麻から繊維までの状態を「フラックス」、繊維を加工した糸以降の製品を「リネン」と呼び分けるのが一般的です。
涼しく湿気が多い地域が栽培にふさわしく、産地として有名な国はロシアやウクライナといった寒冷地が挙げられるでしょう。4月から5月にかけて種をまき、順調に育てば初夏ごろに青紫のきれいな花を咲かせます。それから1ヵ月ほど間をあけて収穫し、フラックスからリネンへと生まれ変わるのです。ちなみにフラックスの種からは良質な油が採取でき、これは食用や塗料として重宝されます。キレイな花を咲かせ、茎は繊維となり、種まで活用できる。フラックスはとても無駄がない植物だといえるのではないでしょうか。
日本では北海道で昔亜麻栽培が盛んだった
日本において、明治時代から本格的に亜麻が生産されるようになった時も、最初の栽培地は北海道でした。戦争が始まると麻製品の大量確保を目的に、亜麻の生産を国ぐるみで行うようになります。しかし戦後を境に少しずつ生産量が減少し、1967年には北海道から亜麻の姿が消えました。
そして現在。北海道では再び亜麻を復活させようと、「亜麻ルネサンス事業」というプロジェクトが推し進められています。
プロジェクトの中心である「(有)亜麻公社」は、北海道札幌市から30kmほど離れた当別町にあります。かつての亜麻栽培を復活させたい、という想いから結成されました。2001年に地元の農家と協力して亜麻栽培を実際に復活させ、現在では毎年7月に満開の花を咲かせる亜麻畑が当別町の観光名所になっています。日本で亜麻の栽培が始まってからおよそ150年。その中心は常に北海道といえるでしょう。
亜麻(フラックス)が生地になるまで
こちらでは亜麻(フラックス)がリネン生地になるまでを解説していきます。生地を作るための亜麻(フラックス)は7月末から8月にかけて収穫され、専用の工場で生地に加工されます。フラックスが生地になるまでの工程は日本と海外でだいぶ違いますので、ここでは日本でのやり方に絞ってご紹介いたします。
亜麻の製造過程その1:浸水 (レッティング)
工場で最初におこなう仕事は、農家からやってきた亜麻(フラックス)を水に浸すことです。
茎の繊維を取りだして加工する前に、まず繊維を取りだしやすい状態にしなくてはなりません。そのためにフラックスを水に浸し、よく発酵させます。すると茎の表皮や柔軟組織といった、生地に使わない部分をバクテリアが分解してしまいます。こうして生地に有用な繊維だけを残す、というわけです。
このようにフラックスを浸水させる手法は「発酵精錬」とも呼びます。精錬とは、不純物を取り出して純度を高める、といった意味合いです。自然な化学反応だけでおこなうこのやり方は、昔ながらの製造方法のひとつ。薬物を使う必要がなく、コストを最小限に抑えられることが大きな利点といえるでしょう。発酵させたフラックスを天日干しにしてよく乾かしてから、次の工程に移ります。
亜麻の製造過程その2:製繊(スカッチング)
製繊とは、浸水と乾燥を経たフラックスから実際に繊維を取り出す作業です。乾いたフラックスの茎を機械にかけて粉砕し、粉々になった硬い部分(木質部)だけを取り除けば、ようやく繊維が手に入ります。
こうして作られたフラックスの繊維は製品工場に運ばれます。そこで紡績の作業を行うことで、とうとう「フラックス」から「リネン」になり、私たちが見慣れたリネンの洋服やタオルの素材ができるのです。
ちなみに収穫できたフラックスがすべてリネンになるわけではありません。たとえば100kgの茎が農家から送られてきた場合、実際にリネンの糸になるのは約15kg。なんとわずか15%程度です。残りは製造の過程で失われるか、燃料や飼料などになります。私たちの元に届くリネン製品は、フラックスからわずかに採れる部分だけを集めて作られているのです。
亜麻の製造過程その3:ドローイング
次の工程は、鉄と木のロールで挟んで鞣す工程です。リネンに艶を出すために行います。これにより繊維として扱いやすくなります。こうすることで、次の紡績で糸がほぐれることなくスムーズに進みます。
亜麻の製造過程その4:紡績(スピニング)
最後の工程です。リネンの場合は水でぬらして紡績(潤紡:ウェットスピニング)をしなければならないことが他の繊維の紡績工程とは違う特徴的な工程です。ゆっくり丁寧に糸にしていく必要があります。
同じフラックスから生まれたリネンでも、生地になるまでの過程でまったく違うかたちに姿を変えます。ここでは種類・織り・染色に分けてリネン生地の詳細を見ていきましょう。
生地になった後の工程
リネン生地の織り
一般的な布の織り方として有名な平織り、綾織りはリネン製品にも多い手法です。衣服を中心にあらゆるアイテムで使われています。
表面に浮かぶ無数のサイコロ目がかわいらしいリネンワッフルは、吸水性と速乾性に優れており、とても衛生的。タオルや枕カバーといったすぐ汚れる日用品ならば、ぜひ選びたいリネン製品です。他にも高級感たっぷりのやわからさがウリの二重織り、あえて粗目に織ってふっくら感を演出したクレープなどがあります。織り方を少し変えるだけでこんなにも豊かな表情を見せてくれるのも、リネンの魅力といえるでしょう。
リネン生地の染色
リネンの染色は、糸から染める先染めと、生地になってからの後染めの2つに分かれます。先染めは糸の段階でしっかり色をつけるため、情緒のある色合いが出しやすいといいます。
後染めは生地を織ってから染色するので、色がつく部分とつかない部分の色ムラが生まれます。この色ムラに味わい深さを感じるファンも多いみたいですね。ハンドや機械でのプリント、最近ではインクジェットプリントなどもあります。
まとめ
リネンがフラックスから生地になるまでを解説してきました。ショップに並んでいるあのリネン製品も、原料の亜麻(フラックス)の状態から手間暇をかけて繊維を取り出し、あらゆる形に加工されています。様々な形や色、風合い、用途で我々の生活に密着しているのがリネンです。ちなみにリネンは塗料を用意すれば自分の手で染め直せます。必要な塗料も最近では通販で簡単に手に入るようになりました。慣れれば自分好みの色合いも自由自在ですので、興味がある方はやってみてはいかがでしょうか。リネンの「できるまで」を学んだあなたが、さらにその先に挑戦するのも面白いかもしれませんね。